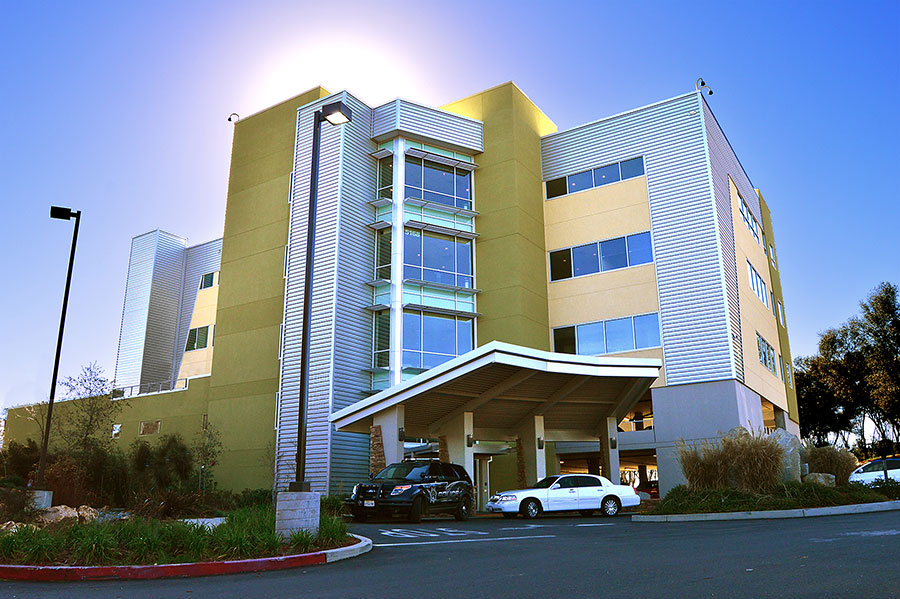
Find the best modular elevator for your project.
A full list of our standard sizes and drawings can be found on our Products Overview page including Holeless Hydraulic, Machine Roomless (MRL) Hydraulic, In-ground Hydraulic, Roped Hydraulic, Machine Roomless (MRL) Traction and Overhead Traction elevators.
Detailed steps to guide you through the design process.
ADA Compliance
All designs are ADA compliant.
Fire Rating
All designs are available in one or two-hour fire rating (for 2-hour, add 1 ¼” to the hoistway outside width and depth). International Building Code requires a two-hour fire rating for elevators serving 4 or more stories or if the elevator penetrates a 2-hour-rated floor. Check with your local authority having jurisdiction (AHJ) for specific requirements within your jurisdiction.
Gurney Compliance
Models SLF and SLFR are gurney compliant for a 24” x 84” gurney with 5” radius corners. Most jurisdictions require that for a building of 4 or more stories, at least one elevator accommodate an ambulance gurney so that EMTs can efficiently remove patients. Some jurisdictions also require gurney compliance for shorter elevators. Check with your local AHJ to confirm requirements.
Custom Sizes
We can also make custom car sizes to meet most needs. To get more design help, contact us and we’ll be happy to discuss your specific project and design something that works for you. If you have a project in mind, reach out for a free quick quote.
We manufacture Hydraulic and Traction elevators, including Machine Roomless versions for both, pre-installed in a hoistway. We also make roped Hydraulic and LU/LA elevators, although these are less frequent. The decision is typically based on overall travel distance; however, there can be other factors, including elevator use patterns and volume. We will not try to talk you into an elevator that does not fit your needs. Here’s a summary of the differences.
Product OverviewIf you’re unsure, contact us and we’ll help you evaluate your project and help you determine the one that is best for you.
Hydraulic
Location
Hydraulic elevators require machine rooms, and Phoenix Modular Elevator offers design help and flexibility in machine room placement. Most often, they are adjacent to the hoistway at the lowest stop. However, they can be on a higher or lower floor and remote from the hoistway.
Remote machine rooms add to the cost, as wires and piping have to run through floors or ceiling. Therefore, we work closely with customers to ensure economical, convenient placement for each project. Note that some jurisdictions require that the machine room be within 10 feet of the hoistway.
Size
Code-required clearances around equipment govern size. In general, the minimum clear interior space must be approximately 4’x10’ or 6’x6’, depending on the door placement and location relative to the hoistway. If you have a preliminary design, contact us and we’ll be happy to sketch up a quick equipment layout to make sure it will work and meet all applicable codes.
Modular Machine Room
Phoenix Modular Elevator also offers a modular machine room which is an ideal option for exterior elevators. It comes with all of the electrical pre-installed, including overhead lights, electrical disconnects and even climate control units. We also pre-install the tank and controller. Our machine rooms are the same footprint as the hoistway, allowing flexibility in placement on the left, right, or rear of the hoistway. The modular machine room does not come with a floor, so a slab will be needed. They bolt to the concrete slab with epoxy anchors.
Machine Roomless
Machine roomless hydraulic elevators contain the machine room equipment inside the hoistway in a compact formation, with a door in the sidewall to enable maintenance access. These elevators require about 20″ additional width, and 12″ additional pit depth to accommodate the equipment. We limit travel to 24 feet due to the smaller tank size. The machine room door cannot open to the exterior.
Traction
Penthouse Traction
Overhead traction elevators require a machine room at the top of the hoistway. It must be 7’ clear height and requires roof access. We build them integral to our hoistway.
Machine Roomless
Machine Roomless (MRL) Traction elevators do not require a machine room, as the motor and sheaves are serviced using the car top. This makes the total hoistway height less than overhead traction. Keep in mind some jurisdictions require full bodily access to the machinery. MRLs do require a controller space, typically a closet located adjacent to the hoistway at the top landing. They can be placed on any floor, although closest to the top adjacent to the hoistway is ideal.
Phoenix Modular Elevator offers a variety of off-the-shelf interior options to fit many budgets. In addition, PME designers are available to help architects specify custom finishes and fixtures for one-of-a-kind projects. We have produced everything from glass elevators to ones with reclaimed barn wood.
Interior Options
- High-pressure plastic laminate walls in your choice of Wilsonart® colors.
- Panelized walls, with your choice of laminate or stainless steel background and laminate or stainless steel panels. We can accommodate almost any configuration of panels and laminate patterns.
- Stainless steel, either #4 satin (the most common selection) or any Rigidized® pattern.
- Raised wood paneling.
- Mirrors and glass can be incorporated into the car, although they are installed on site.
Flooring
We supply standard a plywood subfloor set ¾” below the car sill. The floor is finished by others on site to avoid damage during shipment. The subfloor will accommodate any flooring, but the finished floor needs to be at the level of the sill to avoid a tripping hazard.
Walls
Our standard exterior finish is fiberglass gypsum type X sheathing, which is water-resistant for up to a year in the event a construction project necessitates exposure to the elements. Plywood sheathing is an alternative.
If your elevator is placed on the exterior of a building, or is free-standing and connected via balcony or catwalk, there is an opportunity to make it a design element in your project. Once erected, the hoistway can be finished with any typical exterior product such as brick, stucco or siding.
Some finishes such as wood or steel siding can be factory installed. It depends on whether the finish can survive shipment with no damage.
If your elevator is placed on the interior of a building, it can be skim-coated or sheeted with 1/4″ drywall, and the hoistway walls can serve as interior walls.
Roof
Our standard roof is EPDM (black) or Duro-last (white) rubber roofing. This is glued to a plywood roof and tacked around the sides for shipping. Once the building finish has been applied at the jobsite, the roofing can be terminated. Custom roofs can also be constructed, either in our factory or onsite, to add a high-end look.
Some finishes such as wood or steel siding can be factory installed. It depends on whether the finish can survive shipment with no damage.
PME modular elevators minimize required building modifications for retrofit projects and simplify the design process for new construction.
For travel up to 30′ (3-4 stops), the elevator fits into a single tower. This structure is self-supporting, making it ideal for retrofit/renovation projects.
For travel over 30’ we construct multiple-piece towers in our factory and separate them for shipping. We reassemble the towers onsite and bolt them together. This design is typically not self-supporting and must be tied to the building. If this is not feasible, we can engineer a multi-piece tower to be self-supporting for your application.
If needed, our hoistway can provide some gravity loads for the surrounding building structure. Our elevators are not designed to carry lateral loads or serve as shear walls. Our engineers can coordinate with your engineers to design building attachments.
Pit
Stamped structural drawings and calculations are provided by PME. Your structural engineer will need these when designing the pit and anchorage. You can also use the structural drawings for the building permit.
We will provide dimensions of the pit, but you will need to calculate wall and floor thickness, reinforcement and anchor embedment per site conditions and local codes.
Roof
Most elevator shafts extend above the building roof. Flash around the modular elevator at the roof penetration if the elevator is interior. If the elevator is exterior, it typically butts up to the building. Flash the wall that abuts the building to the roof. Gutters or other drainage systems need to direct water around or away from the shaft.
Walls
The building wall must have an opening for the hoistway door. This can be as narrow as the door, as wide as the entire hoistway front wall, or anywhere in between.
If it is just big enough for the door, the hall stations will need to be mounted in the building wall onsite.
The hall stations are factory-installed in the hoistway wall if the building wall is at least 12″ wider than the door on the hall station side.
The hoistway wall and building wall need to be tied in onsite. You can use simple drywall mud and tape or an expansion joint.
In seismic areas, attach the hoistway to the building so they move together (most common), or separate seismically so if they move separately, they won’t crash into each other. We can provide calculations for the required seismic separation if you choose not to attach them.
Floors
We set the elevator sill to the finished floor level provided to us. There is a 4” beam between the sill and the building floor that is set ¾” below the sill. This allows you to bridge the gap with a plywood subfloor and continue the flooring up to the sill.
We also offer an optional threshold plate that attaches to this beam and bridges the gap. You can use this threshold plate in any application, including seismic areas and to bridge a seismic gap. To avoid trip hazards, flooring in the building and car should be installed flush with the sills.
Sheltering Exterior Doors
If the elevator doors open to the outside, they should be sheltered. Rain and snow can blow in through the cracks around the door and damage equipment inside the hoistway (primarily door equipment and hall stations). Rain can also get into the hall stations and short out the buttons. Wind can blow in debris that can gum up equipment. And direct sunlight can interfere with the door’s safety edge and keep it from closing.
If you can’t or don’t want to build an enclosed lobby, then make sure you have sufficient protection from the elements with overhead canopies, partial side walls, or something similar.
You can also include special hall calls that prevent water damage.
Tie In and FInishingWe hope the Design Overview above will help you choose your modular elevator. It is our goal to make the process as easy as possible. If you have any suggestions or questions, feel free to contact us at your convenience.